I recently gained a miniature metal lathe and milling machine (Hobbymat MD65 & BFE65), its small but a good place to start.
For my first project using them I decided on a hammer to align work in vices and chucks. I wanted a double ended hammer, one end brass and one nylon end, this would give me the ability to tap soft material without damaging it (Using the nylon end) and also tap harder stock (Using the brass end). The design of the hammer must also fit within the work area of the lathe and mill.
This is the design I came up with:
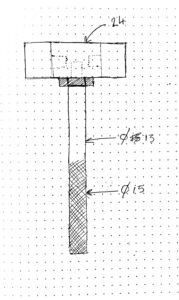
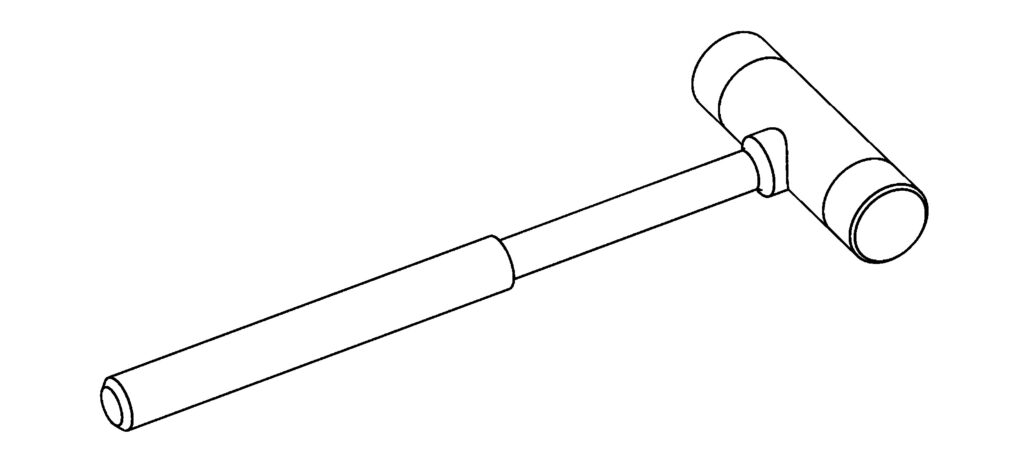
I has a double ended steel head with a threaded on steel handle, knurled at the base. The ends are threaded on to allow easy change when completely damaged.
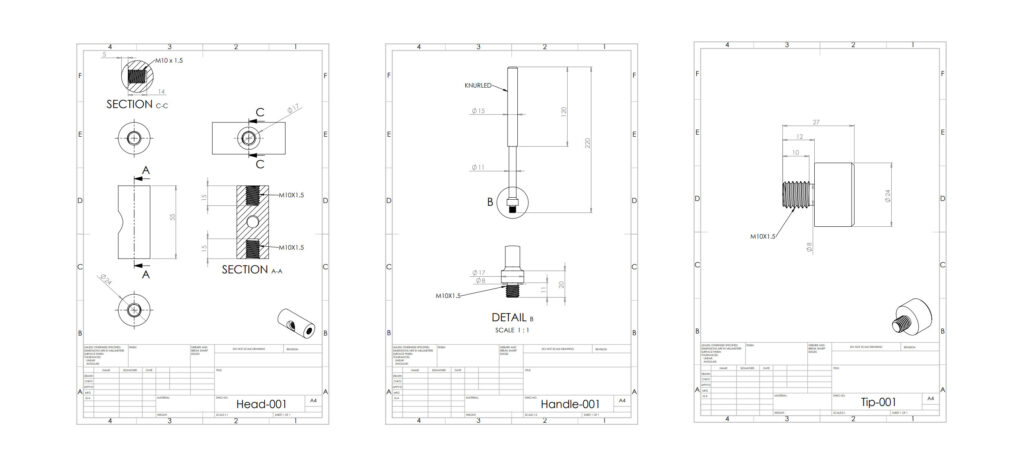
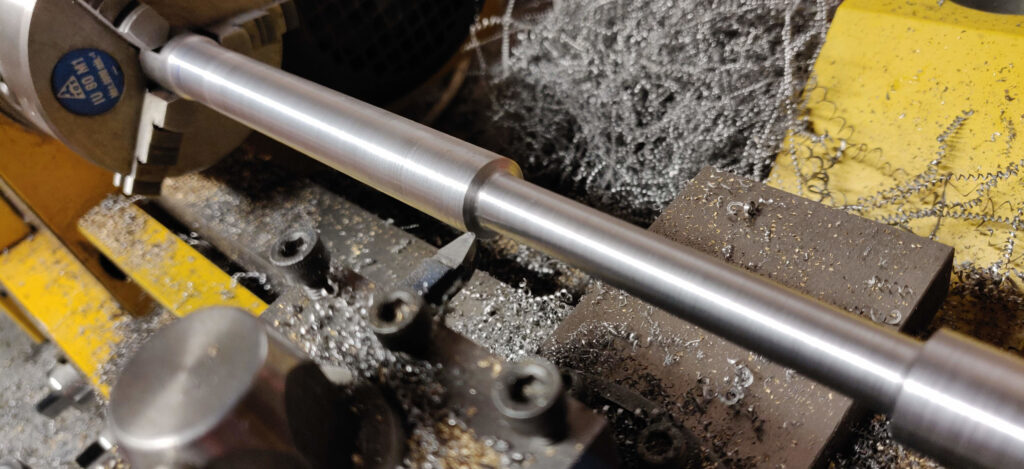
I started with the handle, first taking the diameters close to final dimension using a roughing tool, then switching to a round nosed tool to give a smooth finish to the handle.
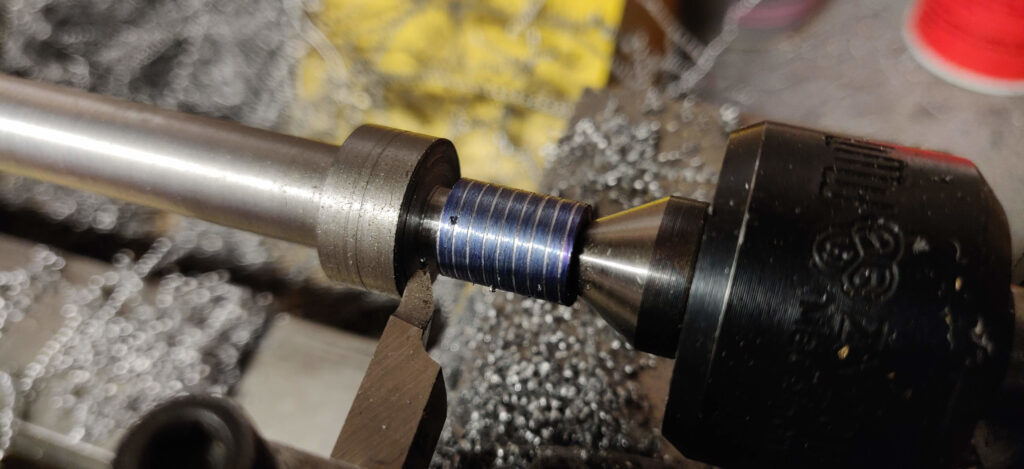
Then, using a 60 degree tool, cut the M10 thread for attaching the hammer head. First with a scratch pass, then when confirmed to be M10, full depth. This part was done by turning the lathe by hand, as having it under power would require the reactions of a fighter jet pilot, also the lathe has no spindle break so would still move after power is removed.
Both tips were cut the same, just at different spindle speeds due to their different material properties.
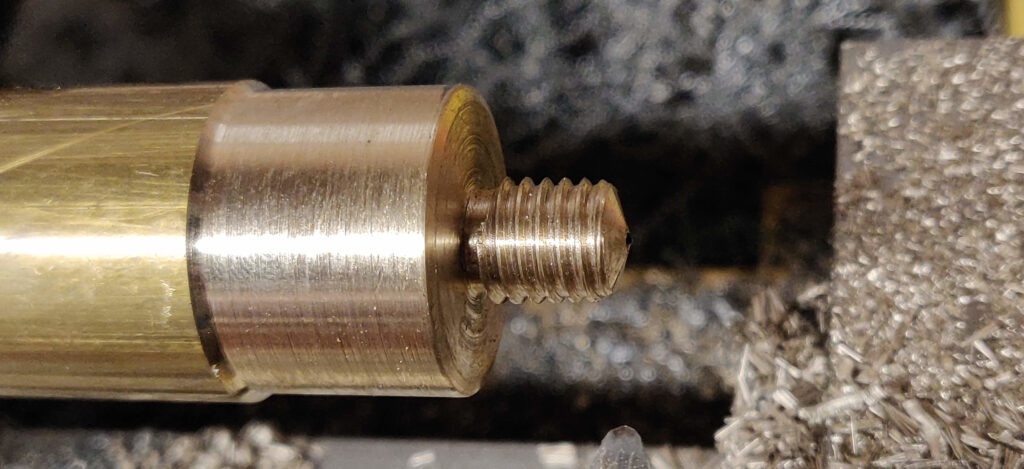
The head of the hammer was a simple enough part to make, the only deviation to the original plan was that I decided to mill a flat on each side of the head to allow me to stamp my initials in and the date.
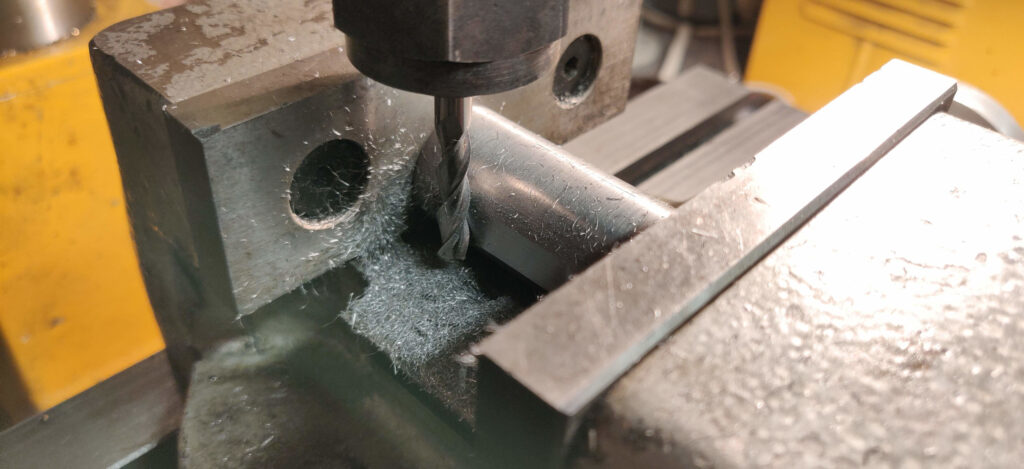
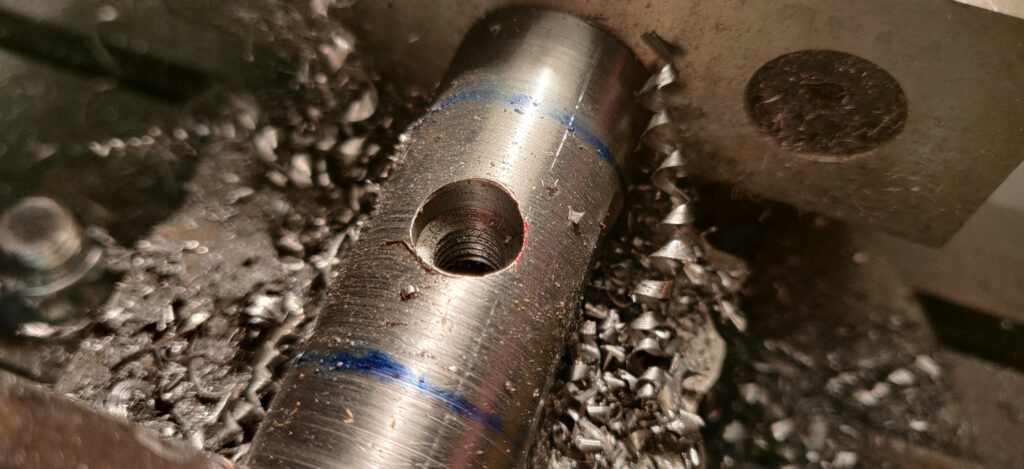
FINAL
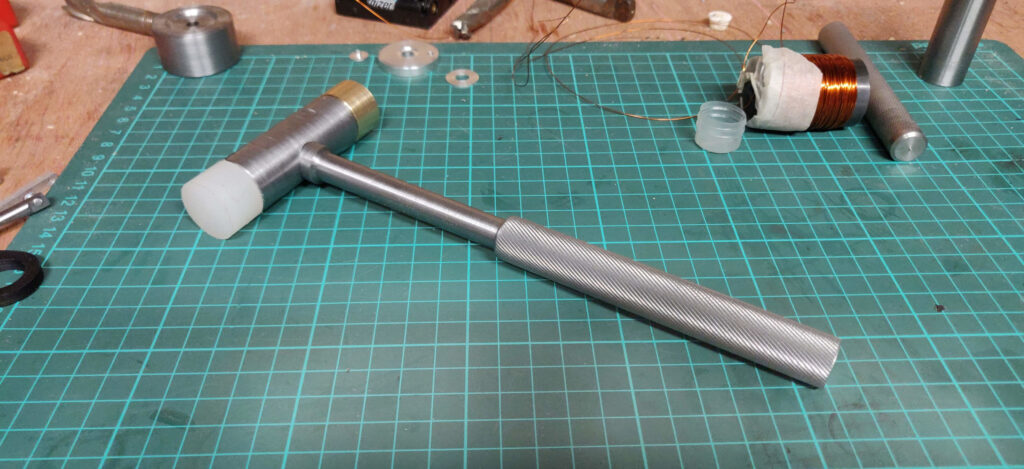
After machining I decided I quite liked the look and feel of the steel in this form. So I just finished it by cleaning it and coating the metal parts in a layer of oil for rust prevention. The tips and handle are secured in by using superglue on the threads, to remove them just apply some heat.
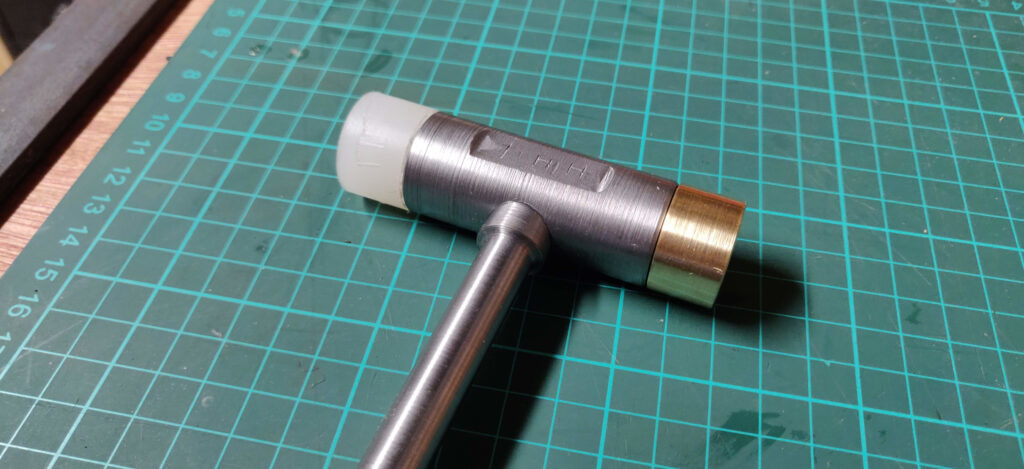
The hammer is so nice I don’t want to use it 🙂
Improvements for next time
- Increase head weight to give a bigger blow.
- Reduce handle weight to give a bigger moment of inertia.
- Engrave my initials using a Dremel rather than stamping. Because while stamping gives a nice font, you only get one change to hit it, aligning the stamp for another blow it difficult.
- Have a deeper knurl on the handle for better grip.
- Have a go at blackening the steel with oil for rust prevention.