To try out the CNC and to check everything is working I created a small test plate, to be machined from wood. Some text to start with, using a 3mm end mill.
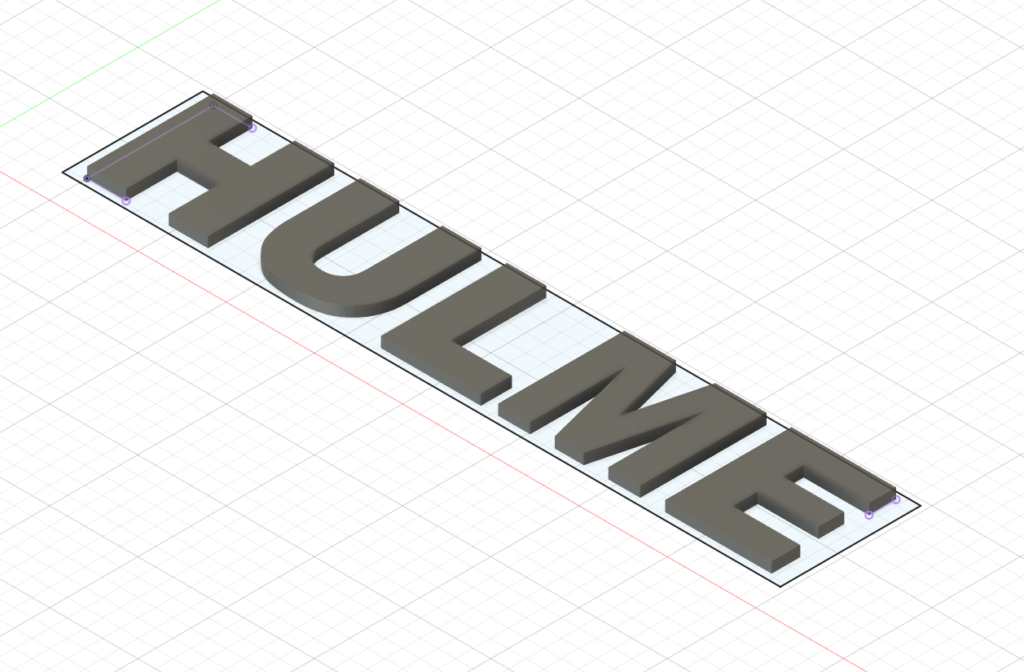
My CAD package of choice is either SOLIDWORKS or CATIA. However for this plate I decided to try out Fusion360 as many people had said how good it is. My first impressions of the software are that it seems adequate enough for 99% of my tasks, however the controls and terminology are something that I’ll have to get used to (Maybe I’ve just been spoiled by SOLIDWORKS and CATIA?). This aside, the reason for trying Fusion360 was because of the built in CAM. This is great because its free and built by a well known company with support if I needed help.
CAM
For this test, I’d be using the 3mm end mill that come with the machine, this’ll create radii on internal corners but as a test piece would be OK.
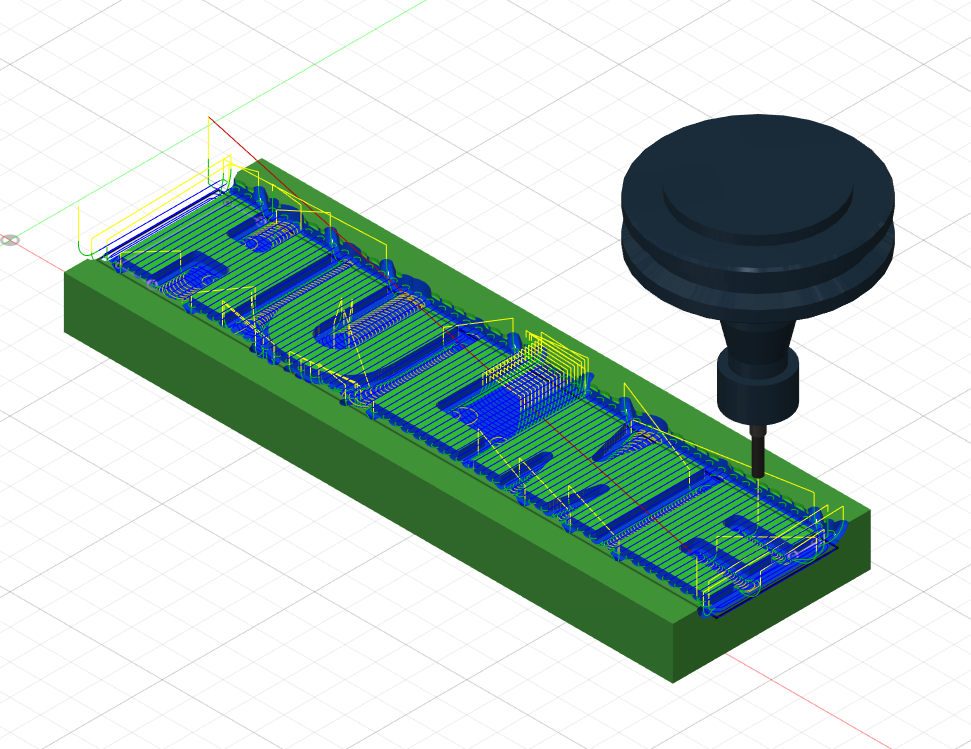
First a facing operation to neaten the top surface, then an adaptive tool path to create the lettering. I started with a large lead-in radius to as not to plunge.
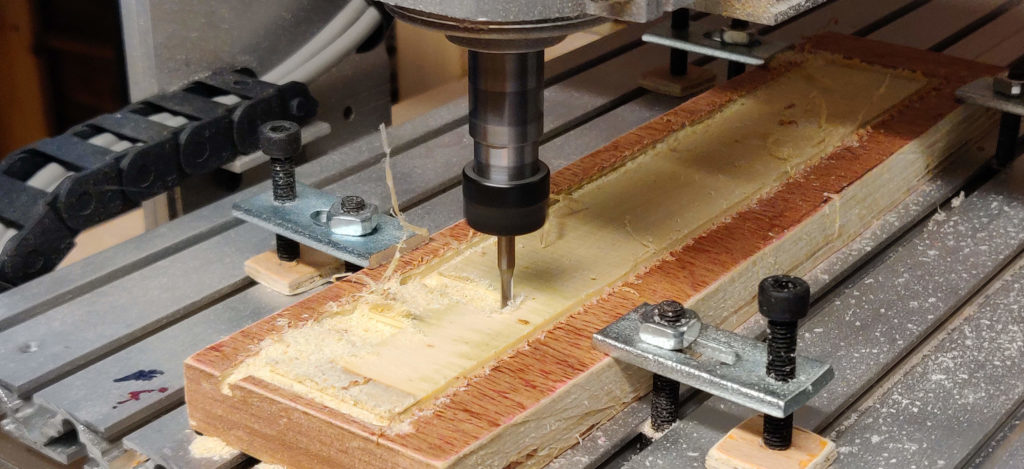
First points to note are that its incredibly noisy and saw dust gets everywhere. Next on the todo list will be an enclosure to contain both the dust and the noise.
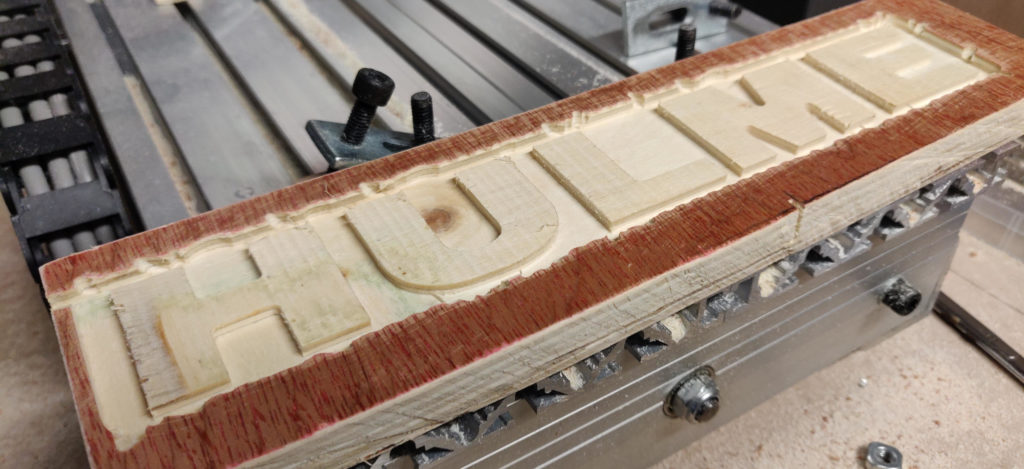
The part turned out OK, however I think the main points to change would have been using a different cutter. The burr created by the end mill is due to it being an up cutter, using a different shaped helix should sort this out, see this great video by Winston Moy on the subject:
The next plan is to machine something bigger, using up the machines full size. Because as the saying goes, go big or go home.